My previous articles were extensively focused on inspections, various types of inspections, and reporting. However, this article takes a slightly different approach. This time, I aimed to clarify the distinct roles and responsibilities of Quality Assurance (QA) and Quality Control (QC) engineers. To achieve this, I have gathered key points about these two crucial terms and compiled them into a single document. This effort is intended to provide a clearer understanding for vertical transportation (VT) professionals and QA/QC personnel alike.
Quality Assurance (QA) Engineer:
- Role: The QA Engineer is a proactive guardian of quality, ensuring that every step in the manufacturing or service delivery process adheres to rigorous quality standards.
- Responsibilities:
- Developing Quality Plans: Crafting detailed strategies to ensure quality throughout the production lifecycle.
- Process Audits: Conduct regular audits to verify that processes are being followed correctly and efficiently.
- Process Improvements: Implementing continuous improvements to enhance efficiency and effectiveness.
- Compliance Assurance: Ensuring that all processes comply with relevant industry standards and regulations.
- Focus: Preventing defects and ensuring processes are efficient and error-free.
- Tools and Techniques:
- Six Sigma: A set of techniques for process improvement.
- ISO Standards: International standards ensure quality, safety, and efficiency.
- Process Mapping: Visual representation of workflows to identify areas of improvement.
- Risk Management: Identifying and mitigating potential risks to maintain quality.
Quality Control (QC) Engineer:
- Role: The QC Engineer is the gatekeeper of the final product’s quality, ensuring that only defect-free, high-quality products reach the customer.
- Responsibilities:
- Product Inspections: Inspecting products at various stages of production to detect defects.
- Testing Procedures: Conducting thorough testing to ensure products meet quality standards.
- Defect Correction: Identifying defects and implementing corrective actions to fix issues.
- Reporting: Generating detailed QC reports documenting the inspection and testing results.
- Focus: Detecting and correcting defects in the final product.
- Tools and Techniques:
- Inspection Tools: Devices used to check the dimensions and quality of products.
- Non-Destructive Testing (NDT): Testing methods that do not damage the product, like ultrasonic testing and radiographic testing.
- Performance Testing: Assessing the product’s performance under different conditions.
- Statistical Process Control: Using statistical methods to monitor and control production processes.
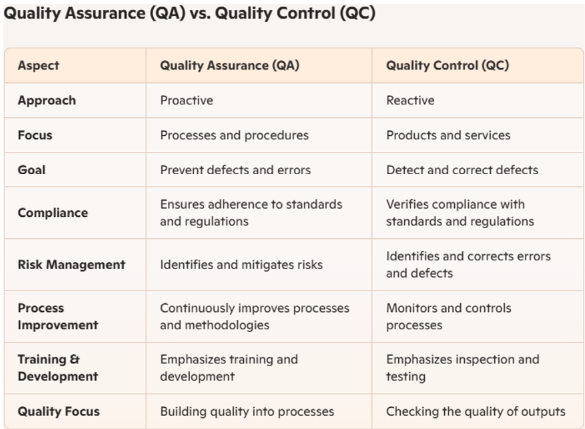
Summary:
- Quality Assurance (QA): Focuses on building quality into the processes to prevent defects and ensure standards are met. It’s about creating an environment where quality is part of the culture and workflow.
- Quality Control (QC): Concentrates on inspecting and testing the final products to find and fix any defects. It’s about verifying that the end product meets the desired quality standards before it reaches the customer.
By clearly delineating these roles, you not only educate laypeople but also provide crucial clarity for QA/QC professionals. This enhanced understanding enables both groups to better grasp and articulate their respective responsibilities. Such clear differentiation significantly contributes to the improvement of overall quality management and operational efficiency, fostering a culture of excellence and precision within the industry.