Elevator system is a combination of electrical, mechanical and electronic parts.
Mechanical systems / parts failures can easily be detected. Even the electrical systems / parts failures can be noticed easily. As in both the cases the parts and their working are visible.
But when it comes to electronics systems/ components it becomes very difficult to get it noticed or detected.
Electronic components’ life gets affected by its design, material composition, maintenance, operational wear and environment conditions.
They are designed to work under prescribed conditions like temperature, humidity and dust.
It is also a known fact that India, having a wide area, has huge variations in climatic conditions. Some parts of the country have extreme cold, some extreme hot and some have extreme humid climates.
A robust design and quality material composition could be considered as a favourable indicator of the reliability and life span of electronic components.
A research study shows that out of heat, humidity, vibrations, and dust, heat affects the electronic components the most.
Heat contributes to 55% of the failures whereas humidity contributes to 19%, vibrations as 20%, and dust as 6%.
Temperature and humidity affect the physical and chemical condition of electronic components. Moist or wet dust can act as a conductor and lead to short circuits.
Transistors may break down or suffer decreased longevity.
The permissible relative humidity level around electronic components is 50%.
It is said that for every increase of temperature by 10°C the life of the capacitor reduces by 50%. The semiconductor’s life also gets affected with an increase in temperature and gets reduced at a faster rate as compared to capacitors.
The electronic components are designed to work between 0-70°C. This needs the surrounding temperature to be maintained around 40-50°C. So that the electronic components’ internal temperature does not exceed the designed temperature upper limit and does not change its characteristics.
There are areas where temperature is very high during summer like, thermal power plants, steel plants, and cement plants, the surrounding temperatures pose a big challenge to the elevator performance.
AC blasts in summer are an example of the effect of increased temperature. ACs are designed for around 50° surrounding temperature. But in present days the surrounding temperature is going beyond 50° centigrade. Certainly, the AC body temperature will be much higher than 50° which can lead to a blast itself.
Hanging the computer after a long continuous working is again an example of the increased heat effect on electronic components.
To maintain the machine room temperature to the required level, we need to ensure proper air circulation through the exhaust fan and cross ventilation. This can be achieved by ensuring proper cooling and a sufficient exhaust system in the machine room.
In addition to the exhaust fan, we must have one exhaust fan attached to the elevator control panel and the VVVF drive unit.
If possible, we can have the machine room air-conditioned.
Dust particles on heat sinks, power connectors, or active devices can act as insulators and can cause overheating.
Dust accumulation affects the reliability of printed circuit boards ultimately reducing the overall useful life of the system.
The dusty atmosphere in cement factories, thermal power houses, and coal mines affects the performance and life of electronic components. The elevator controller needs extra precautions in these areas. Air pressurization of the elevator machine room is the best solution in such conditions.
In addition to dust, contaminated air or water also affects the performance and life of electronic components.
Study shows that the contamination level at 500ug/in2 will lead to a higher rate of failure and faster reduction in life. Whereas contamination levels below 20ug/ in2 will have nearly zero failures.
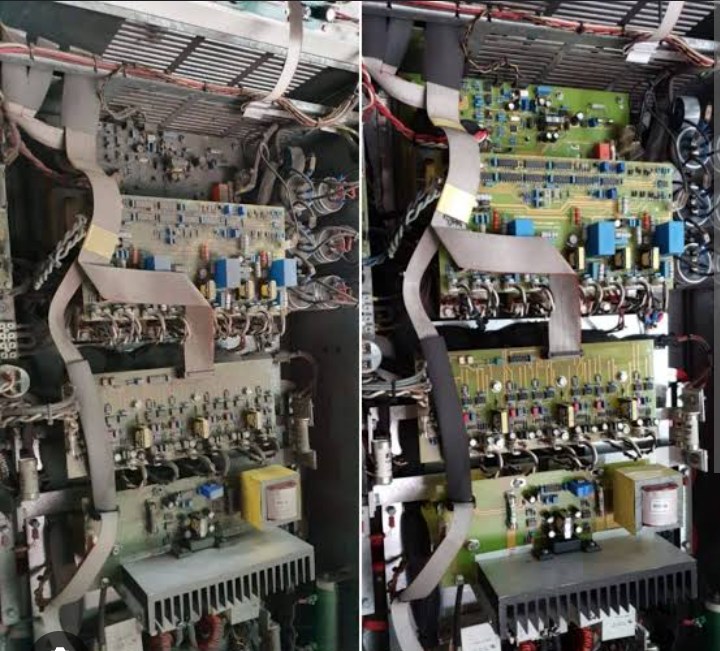
Safeguarding controller to ensure reliability throughout the designed life cycle:
1- Ensure that proper cooling arrangement is made around the controller.
2-Ensure proper and sufficient cross ventilation and exhaust arrangement.
3-Ensure that the exhaust/ cooling fan installed with the controller cabinet is in working condition.
4- Clean the controller component through the blower to avoid dust accumulation.
5- Install dehumidifiers near the control panel.
5-If not able to control the temperature, shut down the elevator for at least 30 minutes during the peak temperature period.